A screw air compressor is a vital component in many industrial applications, providing a reliable source of compressed air. Understanding how it works can help you appreciate its efficiency and functionality. In this FAQ blog, we will explore the working mechanism of a screw air compressor step by step, making it simple to grasp for anyone, whether you’re a seasoned professional or a curious novice.
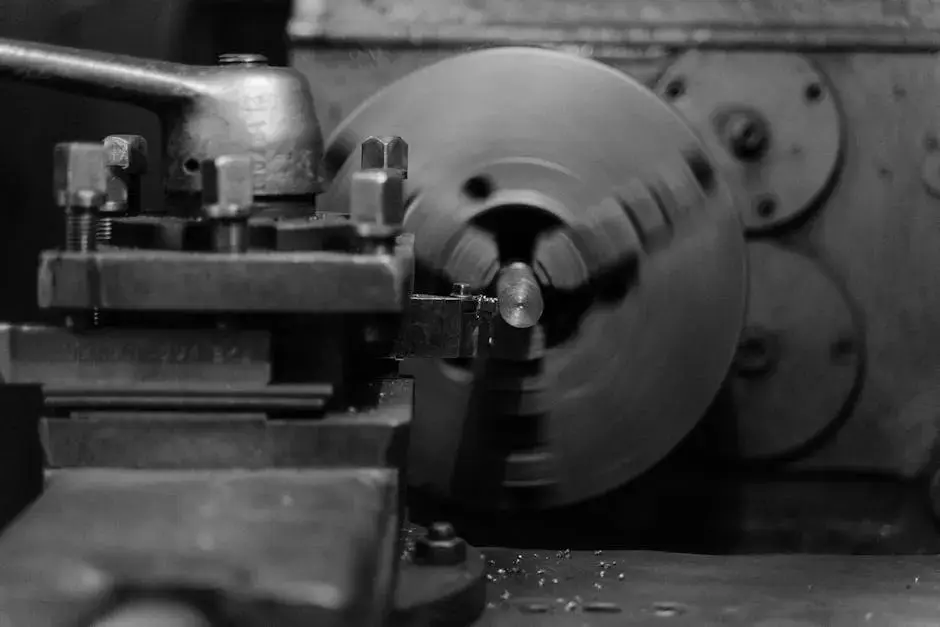
Understanding Compressed Air
Compressed air is an essential utility in various industries, often referred to as the 'fourth utility.' It is versatile, easily transportable, and can power machinery and tools efficiently. To grasp how a screw air compressor works, it's important first to understand what compressed air is and how it's generated.
In essence, compressed air is simply air that is stored at a pressure greater than atmospheric pressure. This involves packing air molecules tightly together, creating a reservoir of energy ready for use. The reliability and usability of this energy depend significantly on the methods and machines used to generate it, like the screw air compressor.
The concept of compressing air might seem straightforward, yet it involves complex physics and engineering principles. By using a screw air compressor, industries can obtain consistent and continuous streams of compressed air that can significantly enhance productivity.
Key Components of a Screw Air Compressor
A screw air compressor is built with several key components that work harmoniously to achieve efficient air compression. The heart of the system consists of two helical rotors, which play a critical role in the compression process. One rotor is male, while the other is female, and they fit perfectly together.
These rotors create a chamber in which air is drawn in. As the rotors spin, the air gets trapped in these chambers and is compressed as it moves from the intake to the discharge side. This unique design allows for a continuous flow of air, making screw compressors more efficient compared to their piston counterparts.
In addition to the rotors, additional components like an inlet filter, a motor, and a cooling system contribute to the overall performance of the compressor. The inlet filter ensures that the air entering the system is clean, while the motor powers the rotors, and the cooling system prevents overheating during operation.
These elements combined create an effective solution for generating compressed air with little to no pulsation, which results in smoother operation for tools and machinery. Understanding these components is pivotal when evaluating the performance and maintenance needs of a screw air compressor.
The Compression Process
The compression process in a screw air compressor is fascinating and highly efficient. When air enters the compressor, it gets pulled into the spaces between the rotors. These rotating helical rotors continuously compress the air without any interruption, which is a significant advantage over other types of compressors.
As the rotors turn, the volume of the air decreases, leading to an increase in pressure. This process is not only effective but also environmentally friendly as it generates less noise and vibration compared to other compressor technologies.
Once the air has reached the desired pressure, it is sent to a storage tank or directly to point-of-use applications. This rapid and efficient compression cycle allows industries to maintain consistent operation and ensures that tools and machines have reliable access to the energy they require.
Furthermore, the continuous operation of screw compressors enhances their longevity and minimizes wear and tear, making them a wise investment for many businesses that rely on compressed air for their operations.
Benefits of Using a Screw Air Compressor
Choosing a screw air compressor comes with numerous advantages that can significantly impact operations in various industries. One of the most notable benefits is their efficiency—screw compressors provide a continuous flow of air, which contributes to higher productivity levels.
Moreover, they have a lower energy consumption compared to other types of air compressors. This reduction in energy use can translate into substantial cost savings for businesses, making it a financially savvy decision to invest in screw technology.
Additionally, screw air compressors are known for their reliability. They can work longer hours without the need for frequent maintenance, which means less downtime and more productivity. The smooth operation also helps minimize wear and tear, extending their lifespan even further.
Another key benefit is their versatility. Screw air compressors can be used across a wide range of applications, from powering tools to running production machinery. This flexibility makes them a favored choice in various settings, including manufacturing, automotive workshops, and construction sites.
In conclusion, the benefits of using a screw air compressor—efficiency, reliability, lower energy costs, and versatility—make it a critical component for many industries looking to uphold high standards of performance.
Wrapping Up
In summary, the operation of a screw air compressor involves a combination of helical rotors that compress air in a continuous and efficient manner. This technology not only improves productivity but also reduces energy costs. By understanding these mechanisms, you can better appreciate the important role screw air compressors play in various industries.