- Ahmed Hessien
- Mar 12
- 4 min read
In the fast-paced automotive industry, efficiency and reliability are key. One of the unsung heroes behind these qualities is the rotary screw compressor. This technology might not be the first thing that comes to mind when we think of cars, but it plays a crucial role in various applications within the sector. In this blog, we'll explore what rotary screw compressors are, how they work, and why they are indispensable for the automotive industry’s success.
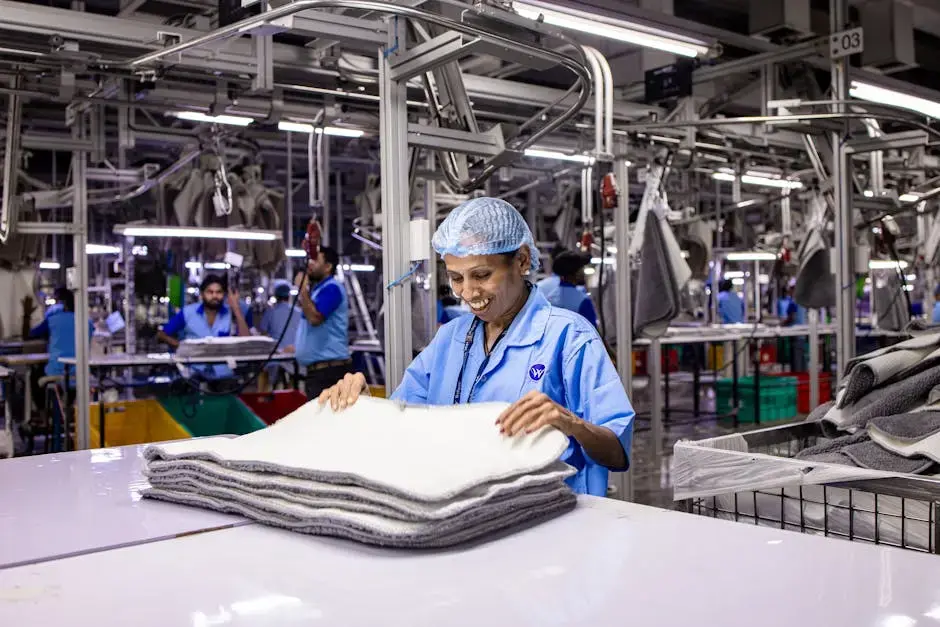
Understanding Rotary Screw Compressors
Rotary screw compressors use two helical screws to compress air, making them incredibly efficient. This section will explain the inner workings of these compressors, their design, and what makes them stand out compared to other types of compressors.
At their core, these compressors employ a simple yet ingenious design. The intertwined screws rotate in such a way that they create a void where air is drawn in, compressed, and then expelled as a high-pressure output. This process is continuous, allowing for a steady flow of air which is crucial for many automotive applications. It's fascinating to see how such a mechanical process can translate to enhanced productivity on the assembly line.
Moreover, the durability of rotary screw compressors cannot be overstated. Unlike positive displacement compressors that often require frequent maintenance, rotary screw models are designed for operational longevity. This attribute makes them particularly appealing to automotive manufacturers, who thrive on minimizing downtimes.
Key Benefits for the Automotive Industry
Exploring the various advantages of rotary screw compressors in the automotive sector reveals just how integral they have become. One of the major benefits is their energy efficiency. By optimizing the air compression process, these compressors lead to significant savings in energy costs, which is crucial for manufacturers looking to improve their bottom line.
In addition to energy efficiency, rotary screw compressors offer a consistent air supply. This is essential during manufacturing processes where fluctuations in air pressure can compromise product quality. With these compressors, manufacturers can ensure a stable and reliable operation, reducing the risk of errors and wastage.
Another noteworthy advantage is the low noise levels associated with rotary screw compressors. In an industry where long hours of operation are the norm, reducing noise pollution can enhance workplace comfort and productivity. This is particularly beneficial in environments where workers are exposed to machinery for extended periods.
Overall, the benefits of rotary screw compressors are multifaceted. They not only enhance the efficiency of production lines but also contribute to a healthier work environment, making them an ideal choice for the automotive manufacturing landscape.
Applications of Rotary Screw Compressors in Automotive Manufacturing
Delving into the specific applications of rotary screw compressors reveals their versatility in the automotive manufacturing sector. They play a critical role in powering pneumatic tools, which are essential for tasks like assembling car parts, tightening bolts, and even in the painting process.
For instance, in paint spraying systems, maintaining consistent pressure is vital for achieving a smooth finish. Here, rotary screw compressors ensure that the paint is applied evenly, reducing the likelihood of defects and improving the overall quality of the vehicle's appearance.
Additionally, these compressors are utilized in the assembly line operations where a reliable air supply is necessary for the proper functioning of various machinery. From the initial stages of manufacturing to the final testing of a vehicle, rotary screw compressors contribute to ensuring that every car meets quality standards.
Furthermore, in terms of flexibility, rotary screw compressors can be adapted for multiple uses throughout the manufacturing process. Their ability to handle varying demands without compromising performance makes them indispensable to automotive manufacturers aiming for high efficiency.
Choosing the Right Rotary Screw Compressor
Selecting the appropriate rotary screw compressor can be a daunting task. With a myriad of models available on the market, it’s essential for businesses to assess their specific needs before making a decision. Factors such as the required air pressure, flow rate, and operational environment play significant roles in this choice.
For instance, understanding the peak demand for air will allow manufacturers to select a compressor that not only meets their needs but also operates efficiently under varying conditions. Moreover, considering the integration of the compressor with existing systems can greatly enhance overall efficiency and reduce operational hiccups.
Beyond technical specifications, businesses should also evaluate the support and maintenance services offered by suppliers. A reliable maintenance plan can significantly extend the compressor's lifespan and ensure it operates at peak performance, benefiting the manufacturer in the long run.
Future Trends in Rotary Screw Compressor Technology
As technology advances, so does the design and functionality of rotary screw compressors. Looking ahead, we can expect innovations that focus on sustainability and energy efficiency to continue shaping this technology. Smart compressors, for instance, are being developed with integrated IoT capabilities that allow for real-time monitoring and data analysis.
These advancements will not only improve operational efficiency but also enable predictive maintenance, thereby reducing the likelihood of breakdowns. By leveraging data, companies can make informed decisions about when to service their compressors, ultimately conserving resources and optimizing performance.
In addition, as the automotive industry pushes towards greener technologies, rotary screw compressors are likely to evolve to meet these standards. Expect improvements in energy consumption and the use of alternative, more sustainable refrigerants in the compressors, aligning them with broader environmental goals.
Ultimately, the future of rotary screw compressor technology looks promising. As they continue to evolve, these compression systems will play an increasingly vital role in the efficiency and sustainability of automotive manufacturing.
Wrapping Up the Importance of Rotary Screw Compressors in Automotive
Rotary screw compressors are more than just mechanical devices; they are vital components that enable the automotive industry to operate smoothly and efficiently. From enhancing production capabilities to ensuring quality control, their role is paramount. As we continue to evolve in automotive technologies, understanding and optimizing the use of rotary screw compressors can lead to greater success and innovation. So, whether you’re part of a manufacturing team or simply curious about automotive technology, keep an eye on these incredible machines!